By Neena Bhandari
Sydney, 06.08.2011 (The Business Times, Singapore): Tom Lane has combined his childhood fascination with building blocks and savvy business acumen to establish Quicksmart Homes that designs, manufactures and supplies prefabricated building modules for high-end readily available accommodation.
“It is the big boys Lego kit. The modules, designed in Sydney and manufactured in China, come complete with plumbing and electrical fittings, carpet and furnishings. They are quick to install, cost effective, and 30 to 50 per cent cheaper than a traditional building”, says Lane, who founded the company in 2007 with just an architect as partner.
He discovered an opportunity to do low cost, high volume, high quality accommodation solutions while expanding his holiday home at Jervis Bay on the New South Wales (NSW) south coast. “I was going the traditional architect – builder way, but found the timeframe and cost for building unsuitable and prohibitive. The pre-fabricated options available were limited”, says Lane, who has capitalised on the shortage of high-quality dwellings.
Today, the company has A$ 700 million worth of tenders to build prefabricated building modules for Australia’s booming resource sector, besides hotels, hospitality, education and health sectors.
While prefabricated materials have also been making waves on Singapore’s shores, the circumstances of its popularity are marked different from Australia’s.
In Singapore, taking the prefabricated route has largely been a government-driven initiative, as it races to reduce the labour-intensive construction sector’s dependence on foreign manpower.
The Building and Construction Authority (BCA), for example, plans to set aside land for factories that make prefabricated parts. It also gave construction firm Tiong Seng a $1 million grant earlier this year to build a facility that makes precast concrete components – a subset of prefabricated materials.
In Singapore, the whimsy of putting together prefabricated materials Lego-style takes a backseat to the increase in productivity that it promises.
What Singapore has in common with Australia’s new fascination with prefabricated houses, however, is the firms that have begun to turn a pretty penny on the promise of houses that are faster and cheaper to put together.
Koon Holdings, for example, bought stakes in two manufacturers of precast materials last year. CEO Tan Thiam Hee estimated that, this year, the use of precast materials in public housing alone will shoot up to 22,000 units from 14,000 units last year.

In Australia, business is similarly booming. Quicksmart Homes has just completed Australia’s first modular healthcare building – a 31-bed orthopaedic and surgical ward extension of the Lake Macquarie Private Hospital in Newcastle (NSW).
Supported on a steel frame, the modules were delivered to the site complete with all fixtures and fittings, infection-reduction tiled flooring, wall tiles and medical gas facilities. Once on site, a nurse’s station, clean utility room, store room and patient lounge were added to the patient room modules.
“The hospital modules are the first of their kind and developed to be lighter and more versatile than large scale steel modular units. The use of modules with medical grade fit outs can deliver outstanding value to healthcare customers. More importantly, it reduces on-site disruption and noise for patients, staff and visitors while the work is in progress”, says the company’s Managing Director, Rufus Harding.
The Quicksmart Homes modular technology is also helping fill the shortage in student accommodation. In the first large-scale application of container-architecture in Australia, the company has completed two modular buildings for on-campus specialised student accommodation at the Australian National University (ANU) in Canberra.
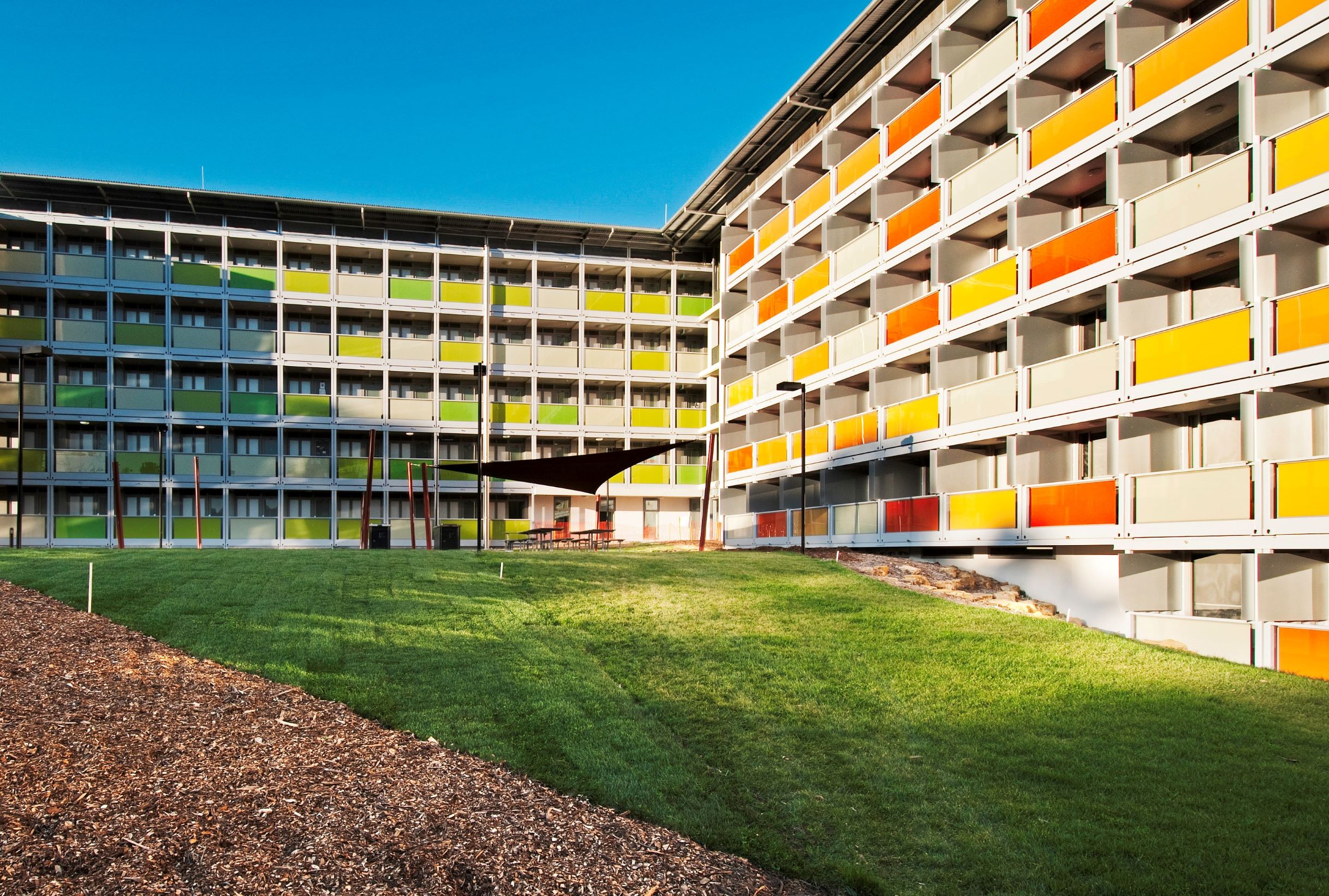
Once the modules arrived at the ANU site, the first six storey installation comprising 70 tailor-made studio and one-bedroom apartments was erected at a rate of one floor a day. The second phase built with the company’s popular studio module, providing a total of 188 new rooms, was ready for use in six months from order to delivery.
The accommodation blocks also won the Australian Capital Territory’s Sustainable Cities Award for Commercial Buildings in 2010. The modules are well insulated, reducing energy needs for heating and cooling. A flexible modular design also makes it easy to recycle, refurbish and extend the building.
The company is also targeting the affordable housing sector, especially in regional areas, with its new Quickshack, a two-bedroom house ready for occupancy within 24 to 48 hours. Made from shipping container parts and clad in timber and Bamboo, the environmentally sustainable unit runs on a plug-in to a rain water tank and a solar hot water system.
Also on the company’s radar is a move into government low-cost housing accommodation and providing disaster recovery modules for an international organisation.
Lane says, “We can keep costs down as our product is factory built. The process and quality of production line mentality in building is very different to the weather and trade dependent traditional building cycle of construction”.
China was the most obvious choice when it came to setting up the factory as he had spent 10 years working on manufacturing high quality handbags for Oroton, the up-market retail group founded in Sydney by his grandfather Boyd Lane 70 years ago.
“It was the same process, but a different product and I was very much at ease setting up the unit west of Shanghai”, says Lane, who has a team of six designers and engineers and six freelance consultants working in its Sydney office.
Quicksmart’s specialised manufacturing unit in China is spread across 150,000 sq. mt., employing over 200 workers. “Once the module shell is built, it is moved to a separate shed on the facility where our team supervises quality control and ensures the internal fittings meet the tough Australian Building Codes. Over 70 per cent of the products that go into the modules are made or owned by Australian companies”, adds Lane.
The company turned over an estimated A$10 million in its first year and has since seen a 50 per cent year-on-year growth. Lane sees phenomenal growth prospects for his product as the demand for affordable, well designed and adaptable housing increases. Enquiries for the product have been pouring in from the U.S, Western European countries and Singapore-based international organisations as Lane heads to Singapore next week.
© Copyright Neena Bhandari. All rights reserved. Republication, copying or using information from neenabhandari.com content is expressly prohibited without the permission of the writer and the media outlet syndicating or publishing the article.